Rehabilitating the Congress Parkway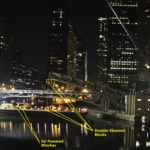
Walsh Construction lifts and lowers 112’ bridge leafs on the Congress Parkway Bascule Bridge with rented air-powered winches, sheave blocks, and telemetry crane scales from Lifting Gear Hire (LGH).
THE SITUATION
Rehabilitating and reconstructing a 60 year old bridge can sound pretty daunting, especially if it hasn’t experienced significant repairs since its creation. And that’s exactly what Walsh Construction had to do for the Congress Parkway Bascule Bridge in Chicago, IL.
The bridge was constructed in the 1950s as part of the national highway development. It had received minor repairs since then, but no major overhauls had ever been conducted. Due to its poor state, in 2010, the Illinois Department of Transportation reached out to Collins Engineering and two subcontractors – Delgado Construction and Walsh Construction – to rehabilitate the four structural steel bascule leafs of the eastbound and westbound bridges. Included in the repairs was a complete replacement of the decking system and the components that open the leafs, which included ensuring the leafs remained balanced, so they may properly open and close uncontrollably.
THE CHALLENGE
In reconstructing an aged conduit, Walsh had to lift 112’ bridge leafs, lock them in at a 70 degree angle, and then lower them back down in a controlled slow manner.
Walsh’s Project Manager, Joe Q., said there were additional challenges that presented themselves during the course of the two-year project.
“The real challenge was keeping traffic open,” Joe explained, “while trying to do the rehabilitation because the eastbound and westbound bridge would have traffic on one set of bridges while we worked on the other. During the construction, we had to maintain boat traffic. During the summer, sailboats passed through twice a week – Wednesdays and Saturdays – we had to ensure that the bridges could be lifted upwards to allow the boats to cross. Keeping the bridge balanced proved challenging, too. Every time we put a piece of steel onto the bridge, the piece of 10 pound steel that was 100 feet away from the pivot arm acted the same as a 1000 pound piece of steel that was 10 feet away from the pivot arm on the back side. So, all these little things because of the nature of the project became exasperated and had to be taken into account and reviewed.”
Aside from a few unexpected issues, all bascule bridges in Chicago have two long trusses that have floor beams that run transverse along the road and grating that goes from floor beam to floor beam. So, pieces of the open grated decking have deteriorated over time, which only made replacing the steel that much more challenging.
THE SOLUTION
To rehabilitate the bridge, Walsh installed an Orthotropic Desk System. While it’s still a structural steel system which consists of two truss arms and floor beams, the steel is of a lighter weight and the floor beams are smaller, so the weight is transferred into the decking system itself. ½ inch flat metal plates and steel webbings underneath give it its structural support. Being a closed system, it’s not exposed to deterioration and doesn’t allow salt or chemicals to fall into the river or down the structural steel and makes for a more maintainable bridge.
During boat session, in order to let the boats pass, Walsh raised three out of the four bridge leafs, locked them in an upwards position while they continued to rehabilitate the bridge as it hung 220 ft in the air. Using a scaffolding system and a crane, Walsh replaced the steel piece by piece.
During the winter months, Walsh jacked the leafs the opposite way to where it could not lift upwards. The 500 ton jacks were used to lift the bridge leafs up a quarter of an inch, so all the weight would go into the temporary support system whereby they could do all the repairs that could not be done while in the up position.
To complete the task, through (the former) Delgado Erectors, Walsh contacted Lifting Gear Hire to figure out what equipment might be needed for the project.
The initial idea was to try and find a winch that could pull the bridge down at a slow and controlled manner, in consideration of the teeter tauter effect, that the bascule bridge functionally operates. It was Walsh’s desire to either co-op or buy a winch that LGH did not offer for rental during that time. LGH informed Walsh that the winch in question was extremely slow in speed (7 ft per minute) and recommended something better that they could rent instead. The winch they ultimately chose was faster but achieved the slower desired speeds by multi-parting the line through some double sheaved blocks. In addition, because they now were using this mechanical advantage, they would not require as large of capacity winch as was initially sought.
Walsh rented and employed the use of two air-powered winches (Thern, TA7-24) by attaching them to a barge on the Chicago River 150’ below the tip of the bridge. Additionally, they used four high tonnage double-sheaved blocks (Shookum, 20-ton WLL, 14” diameter) and telemetry crane scales (supplied by AWS Load and Torque Load Systems) that monitored the forces.
“When we got most of the rehabilitation done,” Joe continued, “we lowered the bridge using the air winches at a controlled measure and finished the project with them down. It was a constant struggle to keep the bridge balanced in order to properly open and close the leafs. We went through a lot of different sized jacks. Different kinds, different apparatuses, different setups, when the team (Lifting Gear Hire) eagerly jumped in and provided not just what we were asking for but other items that were available that could make the job easier.”
THE RESULTS
“Finding a way to control the bridge lowering was a big success,” Joe said. “Each time we did a leaf lowering it was a success. In situations where we had to close down the river, we had to coordinate with the coast guard weeks in advance to set up time frames in order to be able to do this. Each time, it worked out. We had to have backup plans, but we never had to use any of them. Everything worked out without a hitch. Which went to the preplanning that was involved and getting the right people involved including Lifting Gear Hire.”
Beginning in 2010, the project officially wrapped up in 2012 and ultimately, the project was within budget (despite the weather pushing the scheduling back) and was deemed a victory.
“I think everyone including the state would call it a success,” Joe concluded. “I remember driving downtown, 15 years ago, and driving over these road plates that were temporarily placed on top of the bridge and it had pieces of grating that had fallen off which created holes. But now with the new deck system and the rehabilitated bridge, it’s a solid system and now, maintenance issues are a thing of the past. I’m sure the city is quite happy with not having to deal with that anymore. Traffic must be a lot happier with that, too.”
Since that project has been completed, the city of Chicago has sought to rehabilitate the Wells Street Bascule Bridge, the Jackson Street Bascule Bridge, and now upcoming this year is the Adam Street Bascule Bridge which was awarded to Walsh in May 2015.
“I would absolutely use Lifting Gear again,” Joe concluded. “The knowledge and know-how they provided was beyond what I expected of a rental equipment company. They didn’t just help provide what we needed, but recommended other equipment that would help us and explained why we needed it. Lifting Gear Hire was very much a partner to us on this project.”
Equipment Rented:
2 Air-Powered Winches (Thern, TA7-24)
High Tonnage Double-Sheaved blocks (Shookum, 20-ton WLL, 14” diameter)
Telemetry Crane Scales (AWS Load and Torque Load Systems)
About Walsh Construction: Walsh Construction is a subsidiary of The Walsh Group, a 117-year old Chicago-based general contracting, construction management, and design-build firm. The Walsh Group is consistently listed as one of the nation’s top 15 contractors according to Engineering News-Record (ENR). The firm has experience with a wide variety of building, civil, and transportation sectors and maintains regional offices across North America.
About LGH: Lifting Gear Hire is the United States’ largest single organization devoted exclusively to the provision of lifting and moving equipment for rent. LGH holds the most comprehensive inventory for hoisting, rigging, jacking, pulling, material handling, and safety equipment. With over 50,000 pieces, our lifting equipment is available for rent from 19 locations throughout the U.S., and our customers are supported by over 45 Rental Representatives nationwide.